About DFM
Design for Manufacturability (DFM) is all about creating products that are not only functional and high-quality, but also easy and economical to manufacture.
By thinking ahead and designing with real-world production in mind, we reduce costly errors, speed up timelines, and make sure the final product is practical to build—without compromising on performance or aesthetics.
Whether it's simplifying part structures, using standard components, or aligning with existing factory processes, DFM ensures your idea moves smoothly from design to production.
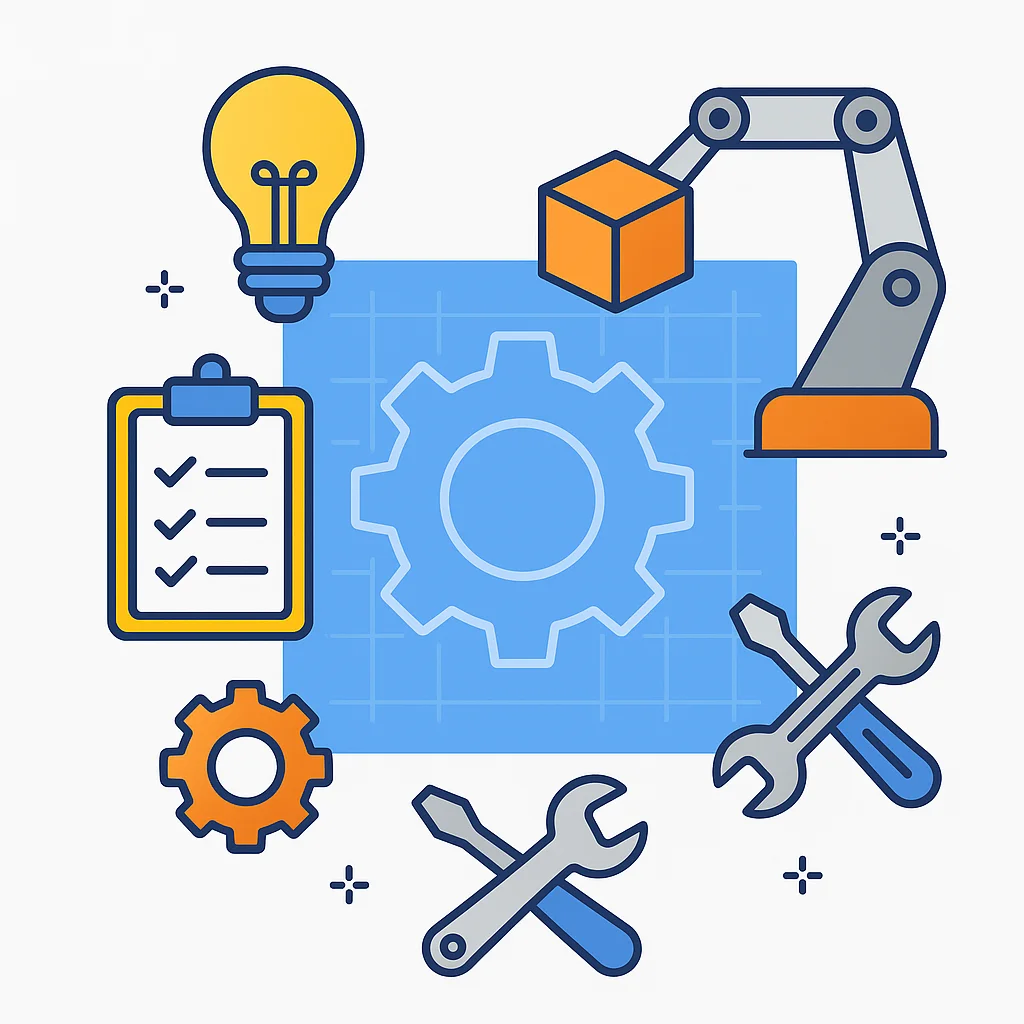
Design for Manufacturability Specifications
📏 Dimensions
- Max PCB size: 250 × 250 mm
- Min PCB size: 9 × 9 mm
- PCB thickness: 1.6 mm / 1 mm
- Thickness tolerance: ±5%
🔩 Copper & Drill
- Copper thickness: 18 μm / 35 μm (custom available)
- Drill diameters: 0.55 – 1.6 mm+
- Drill tolerance: ±0.5 mm
- Min hole-to-hole spacing: 0.45 mm
🔌 Routing
- Track width (standard): 0.254 mm
- Track width (special): 0.16 mm
- Spacing (standard): 0.254 mm
- Spacing (special): 0.16 mm
- Track width tolerance: ±20%
🧩 Clearances
- Pad to track (standard): 0.254 mm
- Pad to track (special): 0.16 mm
- SMD pad-to-pad (standard): 0.254 mm
- SMD pad-to-pad (special): 0.16 mm
- Annular ring (standard): 0.3 mm
- Annular ring (special): 0.2 mm
🎨 Solder Mask & Silk
- Solder mask thickness: 10–25 μm
- Silkscreen min width: 0.254 mm
- Silkscreen min height: 0.254 mm
🎯 Goals of DFM
- Reduce manufacturing cost
- Improve product quality
- Shorten time to market
- Minimize complexity
- Ensure design fits existing manufacturing capabilities
📌 Key Principles of DFM
Principle
Explanation
Minimize part count
Fewer parts = less assembly time, fewer chances for error.
Use standard parts
Standard components are cheaper and easier to source.
Design for ease of assembly
Avoid complicated joining methods or orientations.
Allow for tolerances
Avoid very tight tolerances unless necessary.
Material selection
Choose materials that are easy to machine or mold.
Consider manufacturing processes
Design must align with the limitations and strengths of the process used (e.g., injection molding, CNC machining).
🏭 Where is DFM Used?
- Electronics (PCB design)
- Automotive
- Consumer products
- Medical devices
- Mechanical parts and enclosures
🧠 Why is DFM Important?
If DFM is ignored, the result can be:
- Higher costs
- Delays in production
- Poor product quality
- Tooling modifications or rework
- Production bottlenecks